What’s Inside
ToggleQuality is paramount in Pharma 4.0 with increased quality standards, strict compliance measures, and high safety requirements from the regulated industry. With the highly evolving market trends, organizations are pacing toward digital readiness and quality assurance. Manufacturers are highly vigilant about quality checks during the manufacturing process to ensure they deliver safe products to the market. Manufacturing excellence is thus a challenge with strict adherence to the highest quality standards.
How is pharma manufacturing different?
As pharmaceutical companies directly impact patient health and safety, they are highly under the microscopic lens for the quality and efficacy of their products. According to the WHO, quality control (QC) is a part of the Good Manufacturing Processes (GMP) which ensures that the relevant tests are carried out and the products are not released for sale until the necessary quality checks have been passed.
Why should quality control be done in-process?
With high-quality adherence expectations from pharma manufacturers, quality control measures fall short of their capabilities. The cost of quality control includes possible human errors, equipment failures, abnormal interpretations, and missed analysis/maintenance schedules.
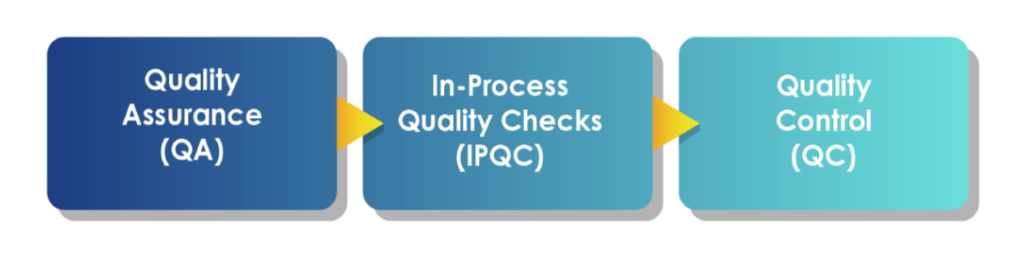
Fig. 1: Quality checks in manufacturing
As the name clearly states, IPQC is in-process quality control, which refers to quality checks during different stages of the drug manufacturing process. It starts from the raw material quality checks to the equipment, production environment, and packaging material. IPQC are regulated, and timely checks that identify any quality mishap in the drug production process and prevent it from affecting the next stage.
In-process quality control in pharma
IPQC stands as an important pillar for quality adherence in the pharmaceutical industry. Since drugs are lifesaving, they hold a greater responsibility to have the right shape, right content, right amount, and the right form.
IPQC is important for pharmaceuticals –
- To detect any loopholes in the drug production process
- To provide real-time monitoring insights
- To enable quick response to identified issues
- To enforce guidelines for drug manufacturing process and packaging standards
IPQC equips a defined set of checks for different drug forms such as oral solid dosages, liquids, and sterile products.
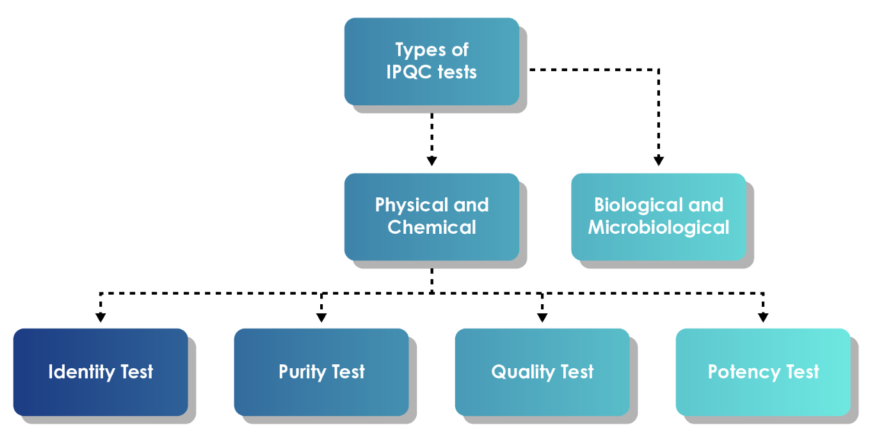
Fig. 2: Types of IPQC tests
Documenting IPQC Results – Still a Manual Dependency
In-process quality control tests are usually frequency-based. Analysts schedule sample analysis to conduct these tests and record observations. However manual handling can lead to missed samples, data inconsistencies, scalability failures, restricted access to reports, and overall facility inefficiencies. A single test result can bring up a report of 200-300 pages depending on the number of batches produced. Maintaining time and test details thus becomes cumbersome and resource intensive.
FDA needs documentation to approve the activities performed, test accuracy, and actions taken. If it is not documented, it has not happened for the regulatory agency.
Steer the Digital Wheel for IPQC Success
Digital is the key to success – for everything and anything today. In-process quality control tests are no exception. Digitalizing IPQC tests accelerates the process, ensuring accuracy and efficiency. Electronic IPQC checks ensure there are no missed sample analysis schedules, maintenance alerts, traceability, and audit compliance. With ‘n’ number of batches produced every day, pharmaceuticals need a digital IPQC system to justify the purpose with precision.
CaliberIPQC – Your Driver for Manufacturing Excellence
Specifically designed to address the modern-day IPQC challenges, CaliberIPQC monitors controls and improves manufacturing efficiency at every stage. It is a robust solution for administering 100% control over IPQC tests. By eliminating manual intervention, CaliberIPQC allows users complete control over product quality with consistent, automated, digitalized in-process quality checks.
It streamlines sample analysis schedules and helps establish predefined test protocols as per business requirements and SOPs. This reduces duplication of tasks. The In-Process Quality Control module generates, and triggers calibration schedules automatically based on the set frequency. By integrating port-based IPQC instruments using a standard RS232 port such as the balance, friability, hardness, thickness, moisture analyzer, and others, data automatically gets registered in the system, minimizing the scope for errors and discrepancies. It also promotes automatic data updates in real time. Moreover, the system allows end users to access the test results on any system, even tablets. CaliberIPQC allows users to generate trend analysis reports of the IPQC data at any time. This enhances decision-making capabilities for efficient business decisions.
If Manufacturing Excellence is your goal, CaliberIPQC must be your shopfloor partner.
Click here to learn more about how CaliberIPQC has helped Zydus, Strides, and many others.